With its innovations for commercial vehicles, international technology company Continental can achieve fuel savings of up to six litres per 60 miles, as a result of the systematic implementation of all technologies available during series production and development.
Continental will be showcasing a diverse, technologically sophisticated, single-source portfolio to attending manufacturers, forwarding agents, and fleet managers. In addition to the latest innovations, visitors will be able to see more familiar Continental technology such as the eHorizon sensor system, which saves almost one litre of fuel over 60 miles, and the ProViu Mirror digital side mirror set, which can help save up to 0.6 litres of fuel.
“We envisage great potential for future optimisation in fleet consumption. Our innovations – some of which are currently in the design phase and some of which are undergoing preliminary development – offer additional potential for reducing consumption by as much as two litres per sixty miles,” explains Nikolai Setzer, member of the Continental Executive Board.
This calculation takes into account more than 20 different technologies that either have recently been implemented in series production or are currently undergoing development. Continental is therefore improving the efficiency of commercial vehicles, cutting CO2 emissions, and improving the cost efficiency of goods transportation.
In 2007, the Member States of the European Union agreed to reduce primary energy consumption by 20% by 2020. Consequently, vehicle manufacturers have an interest in continuing to reduce CO2 emissions. Innovations developed by Continental – e.g. lightweight technologies and efficient exhaust-gas aftertreatment solutions – can help to meet this challenge. Fewer emissions, lower consumption, falling operating costs, increasing payloads, stricter emissions regulations and exhaust standards, such as EURO 6, are constantly driving the development of innovations.
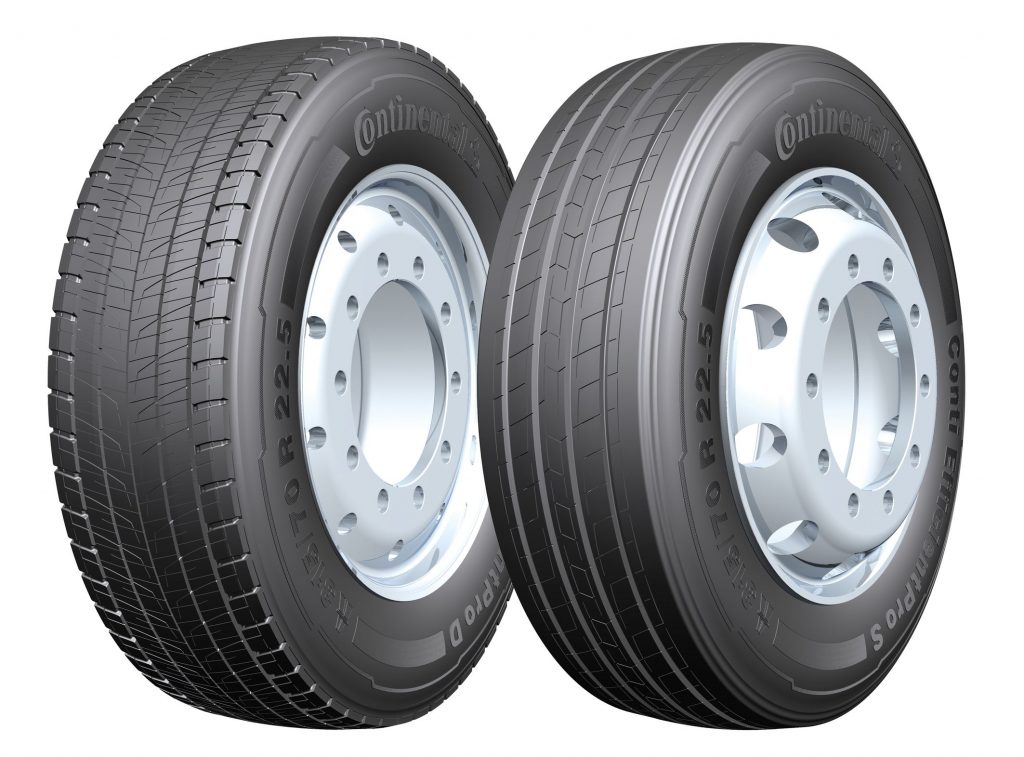
EU “A” label grade: the new Conti EfficientPro fuel-saving tyres
At the IAA Continental will be introducing its new Conti EfficientPro line of tyres for both steering and drive axles. The tyres have been developed specially for long-distance transport on motorways and feature optimised rolling resistance.
In developing the Conti EfficientPro, Continental has built upon tried-and-tested technologies already used in the EcoPlus tyre series. Thanks to special rubber compounds for the multi-ply structure of the tread and optimised rolling properties, the rolling resistance of the Conti EfficientPro has been reduced even further. Compared with the Conti EcoPlus tyre, a 40-metric-tonne semi-trailer truck fitted with Conti EfficientPro tyres on the steering and drive axles achieves additional fuel savings of up to 0.64 litres over 60 miles. Over an annual distance covered of 75,000 miles, this equates to a reduction in CO2 emissions of more than two metric tonnes per year.
The Conti EfficientPro tyres achieve EU label grade “A”, indicating the highest level of fuel efficiency, on account of their low rolling resistance.
Lightweight plastic replaces steel and aluminum
Modern commercial vehicles and buses are subject to exacting demands when it comes to efficiency. To improve the efficiency and cost-effectiveness of goods transportation, payload capacity is to be increased in compliance with statutory limits on axle loads. However, reducing the weight is not just about reducing fuel consumption and, in turn, decreasing operating costs. With the weight-reducing air spring family from Continental, forwarding agents can gain 12–15 kg of payload capacity per axle. With a service life of 400,000 km, CO2 emissions drop by 200 kg as a result. In comparison with conventional steel pistons, this means as much as 75% less weight thanks to the use of a special plastic.
More compact, more efficient, more cost-effective: close-coupled exhaust aftertreatment
Finally, Continental will be unveiling an innovative solution for close-coupled exhaust aftertreatment on heavy-duty commercial vehicles. By positioning the diesel oxidation catalyst (DOC) near the engine, its volume can be reduced by approximately 30%. At the same time, use of the newly developed catalyst substrate in a CS design (Crossversal Structure) enables a further 20% decrease in the amount of materials used and the weight of the DOC. In addition, the diminished heat loss and high conversion efficiency of the innovative CS cell structure will help to meet future nitrogen oxide emission limits, such as the CARB 2023 regulation (CARB: California Air Resources Board) in the U.S.A. Due to the higher working temperature in the DOC, the subsequent injection of urea solution can begin sooner. In addition to the DOC, the solution showcased in Hanover will include the urea metering system integrated in the tank, the SCR (Selective Catalytic Reduction) controller and the metallic catalyst substrate for 100% evaporation of the urea solution.